整厂润滑服务
一、压铸行业面临的问题
1.国际化水平不足:世界有色金属铸件生产的重心向中国转移,但由于压铸工艺水平、技术装备与国际先进水平相比尚有差距,需要有一个提高的过程。
2.环境污染严重:压铸企业发展极不平衡,环保和劳保问题突出,环境污染严重。
3.成本高
利润低:品牌实力不足、科研力量不足、管理上的缺陷均导致国内压铸企业发展后劲不足,受人工工资及原材料上涨影响,利润逐年减少。
二、压铸件生产工艺流程
压铸件订单→ 压铸型设计→压铸型制造→压铸机试模、装模→压铸件脱模→抛丸、喷砂→抛光/研磨、清洗→电镀、喷漆→压铸件粗/精加工→出货
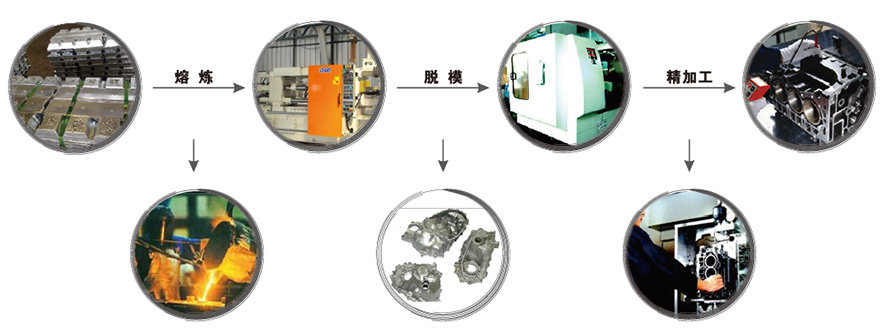
三、压铸行业生产工艺中所遇润滑困惑
1.压铸型精度提不上,切削液选择不当,满足不了精密模具加工要求。
2.压铸件易腐蚀、发霉,大量产品报废,切削液选择不当,解决不了压铸铝合金件的腐蚀及发霉问题。
3.脱模剂离型效果差,脱模剂选用不当,稀释比例不正确,喷涂方法不正确。
4.断刀、断丝锥现象频发,切削液选用不当,稀释比例不正确,满足不了精加工要求。
5.压铸型及压铸机故障率高,脱模剂的选择或使用不正确,液压油的选择或使用方法不正确。
6.生产成本高,竞争力差,选用了多家润滑油供应商,产品参次不齐.
四、骏牌压铸行业润滑清洗产品选型
序 |
加工工艺 |
工艺说明 |
常见问题 |
1 |
压铸模具制造加工 |
模具制造是极为复杂、精密的加工过程,模具的精度 直接决定了产品的精度。模具制造流程涉及到了几十 个加工工序,其中包括飞边、粗磨、铣床加工、钳工 加工、CNC粗加工、热处理、精磨、CNC精加工、电 火花加工、省模等步骤。 |
1.模具制造成本高。 成本增高。 |
2 |
压铸机液压润滑系统 |
压铸机的液压系统犹如人体的心脏, 而液压油则是压铸机的血液。 |
1.油品变黑、油压不稳定。 |
3 |
压铸件脱模 |
金属液体冷却成型后,使用脱模剂及压力设施 将压铸件从模型腔中脱离出来的过程。 |
1.高温合金脱模性差,常出现粘模、卡死。 |
4 |
压铸件清洗 |
清洗研磨抛光出来的压铸件表面残留的污渍。 |
1.清洗性差,不彻底。 |
5 |
压铸件精加工 |
压铸件精加工包括机加工和表面处理两个方面, 机加工包含钻孔、攻牙、铣面等,表面处理包 含电镀、钝化、阳极氧化、电泳、喷粉、喷漆 等。这里重点介绍机加工。 |
1.较难找到一款适用于各种铝合金压铸件加工工艺要求的切削液 |